PADDLE

SRS | PADDLE
A great kayak paddle is usually always characterized by high cost in order to get performance. Until now. Improved hydrodynamics and cost reduction are at the heart of SRS kayak paddle. Twin sheet vacuum forming saves hours of production time for comparably manufactured composite paddle blades. Proprietary foam filling methodologies provide a paddle blade that is robust while reducing part weight.
Completely rethinkg mass production technology for paddles, twin sheet vacuum forming was chosen. To complete this solution cycle, structural foaming of the part was anticipated to render a stiff mono-block structure. This propriatary methodoogy, rendered an extremely light, stiff and robust blade, at vastly reduced cost.
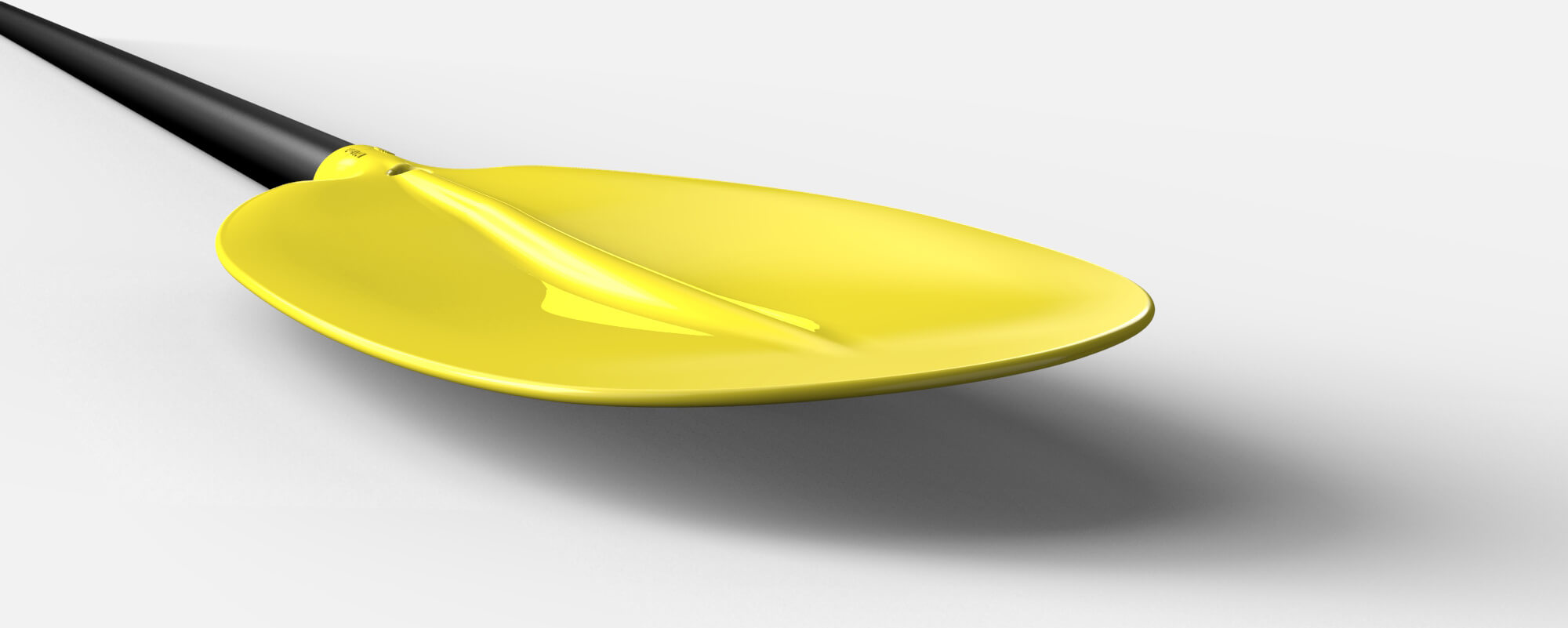
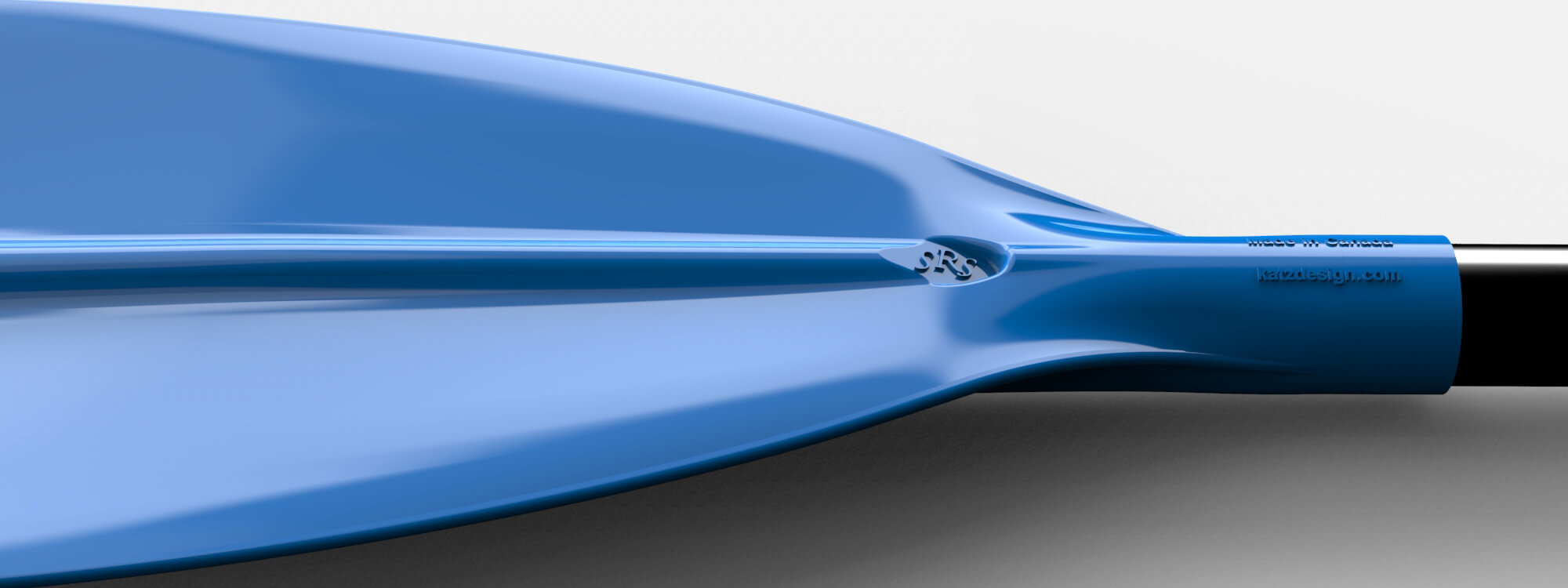
A small branding detail was leveraged to serve as a an anti-rotation feature. Glue holds the blade amply in axial shear while the small logo'd detail nests into a machined notch in the paddle shaft. The paddle to shaft connection is bomb-proof very simple to manufacture.
Surface geometry served multimple design goals. A very metered concave power surface aids the paddler in applying maximum power in the stroke. Additionally the geometry itself served up and incredibly stiff architecture, even without the benefit of structureal foam. The center spline additionally serves to help stabalize the paddle throughout the stroke. A convex back wall is backed off of the front wall to create just enough space for injecting structural foam. Finally, the back tangent surface of paddle shaft provides additioal structure.
